Newsroom
August 4th 2021
Medtech: Healthy Outlook for Australian Innovators
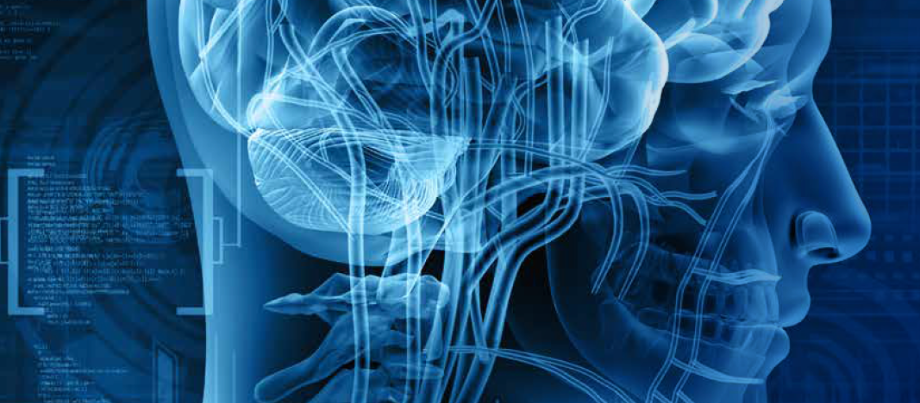
An exciting new R&D facility for innovative medical technology devices, Neo-Bionica will be officially opened in late August in Melbourne. A joint venture between the Bionics Institute and The University of Melbourne, and located in St Vincent’s Hospital, Neo- Bionica actually already commenced operations in June this year. The purpose-built, highly specialised laboratory is equipped with the latest clean-room technology, cutting-edge robotic equipment, enhanced 3D printing and precision engineering tools that are needed to develop and manufacture prototype medical devices for clinical trials.
The driving force behind the new facility, Bionics Institute’s CEO Robert Klupacs, advises that Neo-Bionica will provide Australia with the capability to build clinical-grade medical devices, increasing the speed from initial concept to clinical application. On a site tour of the facility, there’s a cabinet near the entrance displaying a range of medical devices developed by the Bionics Institute in collaboration with other organisations and now by Neo-Bionica researchers.
Among the items on display, there are: an electrode designed to stimulate the vagus nerve, for use in the treatment of inflammatory bowel disease; a Bionic Eye implanted during clinical trials in 2018; EpiMinder’s Minder device, which monitors seizures related to epilepsy and is now undergoing clinical trials; and a Cochlear ear implant, originally developed by the Bionics Institute team.
Neo-Bionica has two clean rooms: one with a Coherent laser cutter; and the other a fully equipped manufacturing workshop, with a Modela Pro-ll MDX-540 3D milling machine, a Ryobi EDP 252 drill press and a HAFCO Metal Master drill press among the range of machines.
Electronics engineer and Neo-Bionica research fellow Alex Thompson says that he “likes making things” and he is certainly in the right place for it. He points to the 3D printers and the resin printer in the second laboratory workshop. There’s a model of a skull on the wall, which Thompson explains was used to stress test implants in the Bionic Eye.
The University of Melbourne’s Chair of Medicine and Director of Neurology at St Vincent’s Hospital, Professor Mark Cook’s consulting rooms are adjacent to Neo-Bionica’s entrance. He says that the new facility will enable clinicians, scientists, engineers and industry partners to collaborate closely in the quest to find solutions for people with hard-to-treat diseases like epilepsy. Professor Cook is leading the medical research team behind Epiminder.
Klupacs advises that Neo-Bionica is set to fast-track treatments for people with epilepsy, urinary incontinence, Crohn’s disease, Parkinson’s disease, Alzheimer’s disease, hearing loss, stroke, arthritis and diabetes. He’s been the Institute’s CEO for more than four years and has more than 30 years of international corporate experience in technology development, mainly in the fields of medical technologies and biotechnology. Trained in pharmacology and biochemistry, Klupacs is also an Australian registered patent attorney and the founder of 33 companies in Australia and Singapore.
“EpiMinder is one of those companies which has come out of the Bionics Institute,” advises Klupacs. “It’s developing Minder, an ultra-long EEG (electroencephalography ) implant to monitor brain activity to improve the standard of care for epilepsy sufferers. Minder monitors the number of seizures in people with epilepsy. Specialists are able to analyse the device’s readings to assess when and how many seizures their patient has had, to assist in epilepsy seizure management. The device will eventually be able to warn people when they are going to have a seizure.
“We were lucky enough to bring Cochlear into the EpiMinder venture as a partner and a major shareholder. EpiMinder is currently undertaking clinical trials for Minder, and we are hoping for FDA (the US Food and Drug Administration) and TGA (Australia’s Therapeutic Goods Administration) approval in two to three years.”
Klupacs adds that in the past, Australia has relied on overseas companies to build prototypes and manufacture the latest medical devices for use in clinical trials.
“One example of this was when we developed a vagus nerve stimulator device for inflammatory bowel disease,” he explains. “We designed it and built a prototype but we had to have it manufactured in Minnesota at a cost of over a million dollars in 2018-19. The US plant had facilities we could not find in Australia, including cleanrooms, documentation and quality systems. And that’s why we have set up Neo-Bionica, to provide that service.
“If you want to get the next generation of Australian-manufactured medical devices, you need a PhD-trained capability, like we have at Neo-Bionica,” he adds proudly. “Our vision is to create a med-tech manufacturing hub in the future.”
While Neo-Bionica will undoubtedly help to lay the foundations for a strong medical devices sector in this country in the years to come, Australian manufacturers have already been moving forward, and
collaborating, on innovative new projects – spurred on in part by the COVID-19 pandemic. Bosch Australia has worked closely on two such projects – one with health technology manufacturer Ellume, and another with Grey Innovation and the Advanced Manufacturing Growth Centre (AMGC) – that are already delivering successful outcomes.
Queensland health technology manufacturer Ellume’s state-of the- art automated assembly lines are being installed at its manufacturing site in Richlands, in south-west Brisbane, this August. Built by Bosch Australia’s Manufacturing Solutions Division (BAMS) team, working closely with Ellume’s engineering team, the two lines were tested at Bosch’s plant in Melbourne, before installation at Ellume’s facility.
A further 16 lines will be built at Bosch and bound for Ellume’s new US production plant in Maryland, scheduled to open later this year. The Washington Post reported on 1 February this year that the US Government had awarded a US$231.8m contract to Ellume to supply 8.5m of its Rapid at Home COVID-19 Tests. These products have been produced in Australia to date, and when the Maryland site is running, it will have the capacity to produce over 15m tests per month.
Ellume’s founder and CEO, Dr Sean Parsons, told the Post that he believes that scaling up production will allow Ellume to reduce the test’s price (currently at US$30 a test). By manufacturing the tests in the US, Ellume will no longer have to ship them from Australia. To date more than one million tests have been shipped from Ellume’s Brisbane plant to the US between February and July this year.
Romulo De Macedo, Head of Engineering at Ellume, is a former project engineer for Bosch, having worked at both its Australian and German plants. Now leading the Ellume assembly team, he explains: “We formed a partnership with Bosch in developing these lines for our Australian and US manufacturing sites, in January last year. Ellume’s Program Manager Steve Carter is overseeing our US site’s build and operations.”
Around 60 Bosch employees and around 30 of Ellume’s employees have been working on building and installing the assembly lines, which will increase production capacity. The lines include end-of- line functional testing to ensure reliable product quality. De Macedo adds that the lines use standard automation equipment such as robots, vision systems, active movers and conveyor feeding systems.
“What is really unique about our lines and a first-of-its-kind is that we combine assembly of standard electronic and mechanical plastic parts with the biological lateral flow assay,” he says. “This is unique, and we have managed to marry the two technologies together. Ellume is also first in the world in developing the COVID home test.”
Dr Scott Fry, Ellume’s Chief Operating Officer, describes the manufacturing process: “The lateral flow assay porous membrane materials, impregnated with biologicals that are produced in-house, are put on reels which are converted to a strip on our automated line. Then it’s assembled onto the electronics and plastics. Everything has to be precisely aligned. Each new line can potentially produce 30,000 to 35,000 Ellume COVID home test kits per day, which will all be bound for the US.
According to Dr Fry, one of the unique features about Ellume’s product is its wireless Bluetooth connectivity. It wirelessly connects to the user’s own smartphone when they are running the diagnostics test. The test data from the user can be shared instantly with public health and with the person’s own GP for subsequent telehealth consultations.
“The Bosch auto lines have a unique wireless contact-free design for programming and testing the device at high throughput,” he adds. “This includes loading the electronics with its firmware and conducting an electronic self-test.”
The home test is suitable for ages two years and over. It’s available for non-prescription home use in the US. The product’s technology enables individuals with or without symptoms to test for COVID-19 infection in 15 minutes, anywhere in the country.
“It’s approved by the US FDA for emergency use, and it is cheaper for consumers to self-test themselves for COVID than pay to visit their GP and to have a test performed at the point of care, or in a laboratory,” says Dr Fry. “The test’s results identify positive cases, and enable public health to know the COVID hotspots and conduct contact tracing. Australia has no legislation for consumer testing of COVID but it is presently under review.
“In the US, it’s about proving safe and effective home tests, which we have done. It’s designed for consumers, and it’s very simple and accurate to use,” adds Dr Fry. “We want to be the global leader for diagnostics home testing for consumers and assist the world to be more prepared for responding to the next pandemic.”
Melbourne-based engineering and technology commercialisation company Grey Innovation led an Advanced Manufacturing Growth Centre (AMGC) industry consortium, supported by a $500,000 Victorian Government grant, to design and produce 2,000 Notus Vivere emergency invasive ventilators to support the fight against COVID-19.
“The project started in June last year and took four months to complete,” advises Jefferson Harcourt, Executive Chairman and Founder of Grey Innovation. “The ventilators were urgently needed for Australian COVID patients and the project retained or created 350 jobs.
“Initially we had approached the Victorian Government with the hypothesis that we would design the ventilators and there would be an overseas manufacturer involved. Then I went to Gavin Smith, President of Bosch Australia, explained the project and asked if Bosch would participate.
“Gavin said ‘Yes’, and by 9am the next day, we had arranged a meeting with the Victorian Government. A budget was approved for a working group to make the emergency ventilators around the clock. We then started calling every manufacturer in Victoria that could make ventilator parts.”
Harcourt negotiated a licence agreement with Smiths Medical in London for a certified ventilator design based on Smiths’ Pneupac Transport Ventilators. The licence agreement allowed a minimum of 2,000 ventilators to be produced by the Grey Innovation consortium of AMGC manufacturers.
At that point, Harcourt advises that the Federal Government came on board with a $32.1m contract for an additional 2,000 ventilators. He says that 2,000 TGA-approved ventilators were sold to the Federal Government, and 200 were sold to the Victorian Government.
The AMGC’s site reveals that it matched the Victorian Government’s
$500,000 investment to support Grey Innovation to manufacture sufficient Notus Vivere Emergency Invasive Ventilators, patient circuits and other consumables suitable for TGA approvals.
Among the many AMGC companies involved, ANCA and Marand manufactured and assembled thousands of critical parts, while Bosch manufactured the test equipment required to verify the ventilators. Harcourt lists the AMGC’s consortium of companies and organisations participating, revealing many of Australia’s leading manufacturers:
Support Partners: Abbe Corrugated, Australian Calibrating Services, Brand Services, BOC, Depth Logistics, EMC Technologies, Esco Industries, Gascon Systems, Hydraulic Seals, Jehbco Silicone Specialists, Kenelec Scientific, Laerdal, Luna Nameplate Industries, National Industries, Novaline, Sutton Tools.
Harcourt has more than two decades of experience in the development and commercialisation of cutting-edge technology as well as the creation and operation of several technology companies. Although Harcourt describes himself as an energetic business entrepreneur, he also attributes part of his success to having a Bachelor’s Degree in Engineering from Swinburne University, before he started the company.
“You couldn’t do this job without engineering qualifications.”
Harcourt is a Director of Tali Digital Limited, and Executive Chairman of GreyScan. TALi, a leading, ASX-listed health business, provides digital attention training for early childhood. GreyScan uses capillary zone electrophoresis (CZE), a technique used for the separation of proteins, peptides, and nucleic acids, to create technology within the security, defence, pharmaceutical and medical industries. Both companies were initially developed by Grey Innovation and Harcourt is very proud of their global progress.
“TALi recently did a partnership deal with The Times Group in India, which has a readership of 400m,” he says. “We will be building the program into the Times online newspapers which has a potential of 50m families to use the TALi program.
“GreyScan was originally designed for explosive detection and we are now pivoting it to see viruses. We are working with CSIRO and the Doherty Institute on a large project where GreyScan can detect the COVID virus (SARS-CoV-2) in people’s breath in just three minutes. This means that we will be able to test people quickly for the COVID virus before they get on the plane, which could be a global break-through for testing COVID and other viruses.”
Carole Goldsmith has shares in Cochlear.
www.neo-bionica.com www.bosch.com.au www.ellumehealth.com www.greyinnovation.com